GN Separation recently fulfilled an order by delivering a batch of decanter centrifuges to a well - known European client deeply involved in large - scale wastewater treatment projects. This accomplishment not only highlights the company's dedication to providing customized industrial equipment but also showcases its capability to meet strict international standards and tackle client - specific operational issues.
Standardized Excellence: Key Characteristics of GN Decanter Centrifuges
The decanter centrifuges delivered are celebrated for their sturdy construction and high - efficiency solid - liquid separation capabilities. They incorporate GN Separation's signature technological innovations. Each centrifuge is equipped with a dual - motor drive system, a proprietary development that allows for precise control of the differential speed between the bowl and the screw propeller.
To combat wear and tear in demanding industrial settings, GN Separation has fitted the centrifuges with tungsten carbide material on the screw blades, feed distribution port, and slag discharge port. This measure significantly prolongs the service life of these crucial components.
Custom - Made to Perfection: Meeting European Standards
In addition to the standard features, this order emphasizes GN Separation's proficiency in customizing its products to suit client needs. The main customizations are as follows:
1. Structural Redesign for Smooth Integration
The centrifuges underwent a structural redesign, featuring a compact and modular frame. This modification was made to fit seamlessly with the client's existing plant layout. It simplified the installation process and enabled retrofitting into confined spaces without sacrificing performance.
2. Premium Motor Selection for EU Compliance
Given the client's focus on regulatory compliance, GN Separation opted for WEG motors. WEG is a globally recognized brand renowned for its energy - efficient and CE - certified electric drives, ensuring that the centrifuges meet European Union requirements.
3. Client - Focused Aesthetic Customization
Understanding the significance of visual harmony in industrial environments, GN Separation provided a range of RAL - standard color options. This allowed the client to select colors that matched their facility's branding or safety protocols.
The European Union has set strict regulations on wastewater discharge, driving up the demand for high - efficiency separation technologies. GN Separation's decanter centrifuges play a vital role in this context, enabling municipalities and industries to achieve the desired solids recovery rates and comply with the standards set by the EU Urban Wastewater Treatment Directive.
This latest delivery to Europe follows a string of successful projects in Southeast Asia, the Middle East, and North America. With this new milestone, GN Separation has proven its ability to offer outstanding engineering solutions and customized co - existence strategies, making significant contributions to global water resource management and industrial efficiency.
- Details
-
Published: 01 August 2025

At GN Separation, we continuously strive to provide high-quality, tailor-made solutions to meet the diverse needs of our global customers. Recently, we successfully delivered a batch of sewage treatment decanter centrifuges to a valued European client, further strengthening our footprint in the European wastewater treatment market.
- Details
-
Published: 31 July 2025
GN Separation has recently completed the successful assembly of two GNLWS364 Three-Phase Decanter Centrifuges. These centrifuges are specifically engineered for solid-liquid-liquid three-phase separation, delivering high efficiency and reliability to a diverse array of industries.
Prominent Features of GN Three-Phase Decanter Centrifuges
The GNLWS364 Three-Phase Decanter Centrifuge distinguishes itself in the market through its well-thought-out design and sturdy build. Here are some of its remarkable features:
1. Uninterrupted and Stable Operation
The GNLWS364 is designed to operate continuously and smoothly for 24 hours a day, guaranteeing non-stop productivity. Its robust components and cutting-edge design minimize the need for downtime and maintenance, making it an excellent choice for environments with high operational demands.
2. Powerful Driving System
This centrifuge is outfitted with a high-performance driving system that ensures consistent and efficient operation. When combined with the high-speed rotating bowl, this system facilitates precise separation of solids and liquids based on their specific gravity differences.
3. Sturdy Construction
The bowl assembly and screw conveyor of the centrifuge are crafted from Duplex Stainless Steel SS2205, renowned for its superior strength and excellent resistance to corrosion. Moreover, the solids discharge port and material distribution nozzle are equipped with Tungsten Carbide inserts, further enhancing the machine's durability and extending its service life.
4. Customizable Separation Parameters
One of the key advantages of the GNLWS364 is its adjustable separation capabilities. Operators can fine-tune the impeller to control the discharge of the "heavy" liquid phase and adjust the pond depth of the heavy liquid during operation. This flexibility enables precise management of the separation process, ensuring optimal results for various material compositions.
Diverse Industrial Applications of Three-Phase Decanter Centrifuges
The GN Three-Phase Decanter Centrifuge is highly versatile and finds applications across numerous industries due to its efficiency and adaptability. Here are some notable examples:
1. Crude Oil Sludge Treatment
In the oil and gas sector, this centrifuge is utilized to separate oil, water, and solids from the sludge in crude oil storage tanks. This process not only recovers valuable oil but also ensures proper disposal of waste materials in compliance with environmental regulations.
2. Residual Oil Extraction from Olive Oil Pomace
The food processing industry benefits from the centrifuge's ability to extract residual oil from olive oil pomace sludge. This maximizes oil recovery while reducing waste, contributing to a more sustainable production process.
3. Fish Oil Extraction
In the aquaculture and fisheries industry, the GN Three-Phase Decanter Centrifuge plays a vital role in extracting high-quality fish oil from fish processing by-products. This extracted fish oil can be used in various applications, such as dietary supplements and animal feed.
GN's Three-Phase Decanter Centrifuges mark a significant leap forward in separation technology. With their ability to operate continuously, robust construction, precise separation capabilities, and adjustable parameters, these machines are poised to revolutionize how industries handle solid-liquid-liquid separation. Whether it's recovering valuable resources from waste materials or ensuring adherence to environmental standards, the GN Three-Phase Decanter Centrifuge is the ideal solution for modern industrial requirements.
- Details
-
Published: 25 July 2025
GN Separation has recently proudly announced the successful completion of factory trial runs for its newest batch of High-Frequency Fine Vibrating Screens. The order, consisting of the GNFG1440 model, is now ready for shipment to a major overseas client, where these screens will play a crucial role in supporting onsite operations.
Design: The Foundation of Performance - The GNFG1440 Model
The GNFG1440 High-Frequency Fine Vibrating Screen is primarily designed for wet screening and dewatering applications. Powered by two long-stroke vibration motors, the equipment employs a reverse self-synchronization principle to generate precise, high-frequency vibrations. This innovative design ensures a linear motion path, facilitating optimal material stratification and significantly enhancing screening efficiency for fine-grained particles. With its compact yet sturdy construction, the GNFG1440 is perfectly suited for industries that demand high throughput and accuracy, such as mining, coal preparation, and metallurgy.
Key Features and Technological Innovations
1. Superior Structural Integrity with Q245R Steel
The screen deck of the GNFG1440 is crafted from Q245R high-strength steel, a material known for its excellent weldability and durability, surpassing that of conventional Q235 steel. After assembly, the entire screen box undergoes stress-relief heat treatment, effectively eliminating residual welding stresses and minimizing the risk of deformation. This process guarantees long-term structural stability, even under continuous heavy-duty use.
2. Reliable Performance with International-Brand Vibration Motors
To ensure consistent and reliable performance, GN Separation has equipped the GNFG1440 with world-class vibration motors sourced from leading manufacturers. These motors are engineered for low-maintenance operation, reducing downtime and lowering lifecycle costs.
3. Long-Lasting Protection with Polyurea Coating
The screen deck is protected by a polyurea spray coating, renowned for its exceptional resistance to chemicals, moisture, and abrasion. This coating significantly extends the equipment's service life compared to traditional paints or epoxy resins, ensuring reliable performance in corrosive environments such as coal slurry processing or mineral tailings handling.
4. Easy Maintenance with Modular Screen Frame and Polyurethane Flexible Screen Mesh
The GNFG1440 features a multi-segment screen deck that simplifies maintenance and screen mesh replacement. Its design accommodates polyurethane flexible screen meshes, which offer superior durability and elasticity compared to metal screens. Additionally, the frame supports optional spray pipe assemblies for automated screen cleaning, preventing clogging and maintaining optimal screening efficiency.
5. Smooth Material Flow with Buffer-Enhanced Feed Box
The equipment's feed box adopts a modular design with multiple integrated buffer plates. These plates dissipate the kinetic energy of incoming materials, reducing impact stress on the screen surface and extending component lifespan. A rubber-lined interior further protects the feed box from wear, minimizing the need for frequent repairs.
Diverse Applications in Wet Processing Industries
The High-Frequency Fine Vibrating Screen is engineered to excel in a variety of wet screening, classification, and dewatering tasks across multiple sectors:
- Mineral Processing: Efficiently separates fine ore particles in gold, copper, and iron ore beneficiation plants.
- Coal Preparation: Dewaters coal slurry to produce clean, market-ready coal products while minimizing water content.
- Metallurgical Industries: Classifies and dewaters tailings, reducing environmental impact and enabling water recycling.
- Chemical and Construction Materials: Processes quartz sand, limestone, and other fine-grained materials with precision.
Global Market Expansion and Client-Focused Innovation
GN Separation's latest accomplishment highlights its strategy of integrating localized R&D with global supply chain expertise. By working closely with clients to understand their operational challenges, the company customizes solutions like the GNFG1440 to meet specific industry demands. For more information, please feel free to reach out to GN Separation.
- Details
-
Published: 20 July 2025
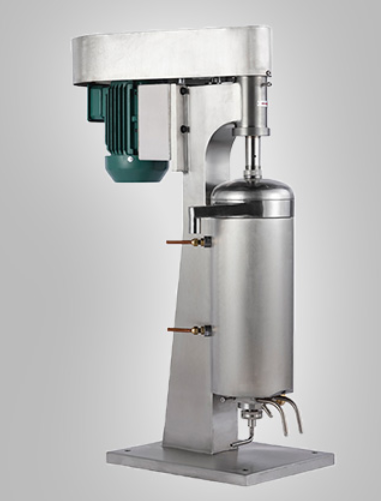
When it comes to clarifying liquids with low solid content or separating fine particles, tubular centrifuges offer a practical and reliable solution. At GN Separation, the high-speed tubular centrifuge is designed to provide consistent performance for applications in a range of industries, including food and beverage, chemical processing, and biotechnology.
- Details
-
Published: 16 July 2025
Recently, GN Separation successfully finished manufacturing two sets of GNOST-15 Oil Sludge Treatment Systems (OSTS). These systems are now going through rigorous factory trial assemblies to guarantee top-notch performance before being deployed.
A Holistic Approach to Oil Sludge Treatment
The GNOST-15 oil sludge treatment system consists of seven interconnected modules, each designed to carry out specific functions. Together, they convert toxic oil sludge into reusable resources. The system effectively tackles issues like high solid content, emulsified oils, and varying viscosity, ensuring efficient separation of oil, water, and solids while keeping operational costs and environmental impact to a minimum.
1. Slurry Feed Pump Module: Precise Delivery for Continuous Processing
The slurry feed pump module marks the starting point of the system, transporting raw oil sludge into the treatment sequence. It is fitted with high-pressure, corrosion-resistant pumps that guarantee a steady flow of material, even in tough conditions.
2. Pre-Mixing Tank Module: Intelligent Conditioning for Better Separation
Raw oil sludge often contains emulsified oils and dense solids that make direct separation difficult. The pre-mixing tank module addresses this by diluting and conditioning the feed through controlled stirring, temperature control, and chemical addition. The integrated steam generator module produces steam to heat the sludge to ideal temperatures (usually 60–80°C), breaking down thick emulsions and improving flow. This step is vital for preparing the sludge for subsequent processes, ensuring higher separation efficiency.
3. Shale Shaker Module: Precise Removal of Large Solids
To shield downstream equipment from damage and blockages, the shale shaker module employs a high-frequency shale shaker to eliminate coarse solids (>2 mm). The shaker is equipped with an anti-splash cover and spray nozzles to prevent material from escaping and ensure uninterrupted operation without manual assistance. This module lightens the load of solids on subsequent centrifuges, extending their lifespan and boosting performance.
4. GNLW-554 Two-Phase Decanter Centrifuge Module: Fine Solid Separation for Cleaner Output
The GNLW-554 two-phase decanter centrifuge is a key part of the system, using centrifugal force (up to 3,000 G) to separate fine solids from liquids. By adding flocculants during operation, the module achieves outstanding solid removal rates (>95%), resulting in an oil-water mixture with reduced solids content. This step is crucial for enhancing the efficiency of the final oil-water separation stage.
5. GNLWS-554 Three-Phase Centrifuge Module: Maximizing Oil Recovery
The GNLWS-554 three-phase centrifuge module stands at the forefront of oil-water-solid separation technology. It uses differential speed control and a sophisticated bowl design to efficiently split the incoming mixture into three streams: recovered oil, treated water, and residual solids. This module not only ensures adherence to environmental standards but also allows clients to recover valuable hydrocarbons, boosting project profitability.
6. Chemical Dosing Module: Tailored Formulations for Peak Performance
Given that oil sludge composition differs greatly across industries, GN Separation's chemical dosing unit enables real-time adjustment of treatment parameters. Operators can prepare and inject demulsifiers, pH adjusters, and flocculants in precise amounts using pumps.
7. Steam Generator Module: Energy-Efficient Heating for Improved Process Efficiency
Heating plays a pivotal role in breaking emulsions and reducing viscosity. The steam generator module generates clean, dry steam to heat the pre-mixing tank and maintain optimal process temperatures.
Factory Trials: Ensuring Dependability in Real-World Scenarios
The two GNOST-15 systems are currently being assembled for factory trials at GN Separation's facility in China. By blending robust engineering with a modular design, the company provides scalable solutions tailored to various client requirements. For further details, please don't hesitate to get in touch with us.
- Details
-
Published: 12 July 2025