Recently, GN Separation successfully finished manufacturing two sets of GNOST-15 Oil Sludge Treatment Systems (OSTS). These systems are now going through rigorous factory trial assemblies to guarantee top-notch performance before being deployed.
A Holistic Approach to Oil Sludge Treatment
The GNOST-15 oil sludge treatment system consists of seven interconnected modules, each designed to carry out specific functions. Together, they convert toxic oil sludge into reusable resources. The system effectively tackles issues like high solid content, emulsified oils, and varying viscosity, ensuring efficient separation of oil, water, and solids while keeping operational costs and environmental impact to a minimum.
1. Slurry Feed Pump Module: Precise Delivery for Continuous Processing
The slurry feed pump module marks the starting point of the system, transporting raw oil sludge into the treatment sequence. It is fitted with high-pressure, corrosion-resistant pumps that guarantee a steady flow of material, even in tough conditions.
2. Pre-Mixing Tank Module: Intelligent Conditioning for Better Separation
Raw oil sludge often contains emulsified oils and dense solids that make direct separation difficult. The pre-mixing tank module addresses this by diluting and conditioning the feed through controlled stirring, temperature control, and chemical addition. The integrated steam generator module produces steam to heat the sludge to ideal temperatures (usually 60–80°C), breaking down thick emulsions and improving flow. This step is vital for preparing the sludge for subsequent processes, ensuring higher separation efficiency.
3. Shale Shaker Module: Precise Removal of Large Solids
To shield downstream equipment from damage and blockages, the shale shaker module employs a high-frequency shale shaker to eliminate coarse solids (>2 mm). The shaker is equipped with an anti-splash cover and spray nozzles to prevent material from escaping and ensure uninterrupted operation without manual assistance. This module lightens the load of solids on subsequent centrifuges, extending their lifespan and boosting performance.
4. GNLW-554 Two-Phase Decanter Centrifuge Module: Fine Solid Separation for Cleaner Output
The GNLW-554 two-phase decanter centrifuge is a key part of the system, using centrifugal force (up to 3,000 G) to separate fine solids from liquids. By adding flocculants during operation, the module achieves outstanding solid removal rates (>95%), resulting in an oil-water mixture with reduced solids content. This step is crucial for enhancing the efficiency of the final oil-water separation stage.
5. GNLWS-554 Three-Phase Centrifuge Module: Maximizing Oil Recovery
The GNLWS-554 three-phase centrifuge module stands at the forefront of oil-water-solid separation technology. It uses differential speed control and a sophisticated bowl design to efficiently split the incoming mixture into three streams: recovered oil, treated water, and residual solids. This module not only ensures adherence to environmental standards but also allows clients to recover valuable hydrocarbons, boosting project profitability.
6. Chemical Dosing Module: Tailored Formulations for Peak Performance
Given that oil sludge composition differs greatly across industries, GN Separation's chemical dosing unit enables real-time adjustment of treatment parameters. Operators can prepare and inject demulsifiers, pH adjusters, and flocculants in precise amounts using pumps.
7. Steam Generator Module: Energy-Efficient Heating for Improved Process Efficiency
Heating plays a pivotal role in breaking emulsions and reducing viscosity. The steam generator module generates clean, dry steam to heat the pre-mixing tank and maintain optimal process temperatures.
Factory Trials: Ensuring Dependability in Real-World Scenarios
The two GNOST-15 systems are currently being assembled for factory trials at GN Separation's facility in China. By blending robust engineering with a modular design, the company provides scalable solutions tailored to various client requirements. For further details, please don't hesitate to get in touch with us.
- Details
-
Published: 12 July 2025

GN Separation is pleased to announce the successful shipment of two complete GNOST-15 oily sludge treatment systems to a valued client in Asia. These systems are designed for the efficient separation and recovery of oil, water, and solids from a variety of oily sludge sources such as refinery waste, tank bottom sludge, and drilling waste.
- Details
-
Published: 11 July 2025
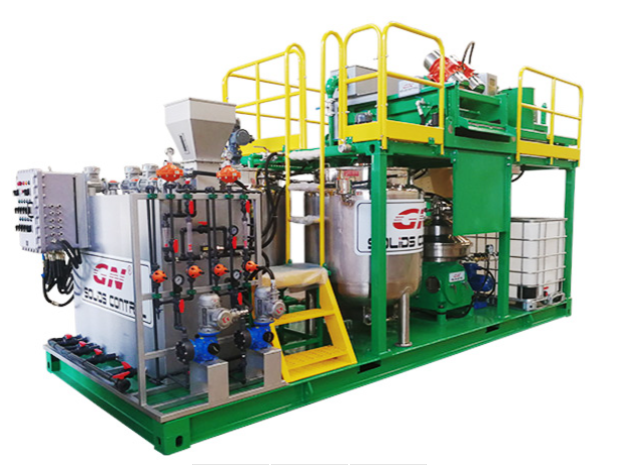
Managing oily sludge has long been a challenge for refineries, drilling sites, and industrial plants due to its complex composition and environmental risks. GN Separation offers a comprehensive Oily Sludge Treatment System designed to address these challenges with efficiency, environmental compliance, and resource recovery in mind.
- Details
-
Published: 27 June 2025
GN Separation has recently completed the assembly of a 3-phase decanter centrifuge, specifically the GNLWS554 model. This centrifuge is slated for shipment to the United States, where it will be employed in the treatment of oily sludge.
The Significance of 3-Phase Decanter Centrifuges in Oily Sludge Treatment
Oily sludge, an inevitable byproduct of oil extraction, refining, and storage processes, presents a formidable environmental challenge. Its intricate composition, comprising oil, water, and solid contaminants, makes traditional treatment methods inadequate. These conventional approaches often fail to achieve efficient separation, resulting in escalated disposal costs and non-compliance with environmental regulations.
In contrast, 3-phase decanter centrifuges offer a streamlined solution for oily sludge treatment. They excel in precisely separating oil, water, and solids in a single step. By harnessing centrifugal force, these machines expedite the natural gravitational separation process. This not only enables industries to recover reusable oil but also significantly reduces the volume of solid waste. The GNLWS554 model, tailored for harsh industrial conditions, overcomes the limitations of traditional systems by optimizing separation efficiency and ensuring operational reliability.
Notable Features of GN’s GNLWS554 Three-Phase Decanter Centrifuge
Dual-Motor Drive with VFD Control for Precise Separation
The GNLWS554 is equipped with a dual-motor drive system, which allows for independent control of the bowl and scroll speeds through a Variable Frequency Drive (VFD) control cabinet. This configuration empowers operators to fine-tune the differential speed between the bowl and scroll, ensuring optimal separation performance even under varying feed conditions.
Tungsten Carbide Wear Protection for Prolonged Lifespan
Given the abrasive nature of oily sludge, GN Separation has incorporated robust wear protection in the GNLWS554. Critical components, such as the scroll flights and discharge ports, are reinforced with tungsten carbide alloy tiles and protective sleeves. This design extends the service life of the centrifuge, reduces lifecycle costs, and ensures uninterrupted operations for clients.
Centripetal Pump Design for Easy Phase Interface Adjustment
The GNLWS554 features a centripetal pump system that enables real-time adjustment of the light (oil) and heavy (water) liquid phase interfaces during operation. This functionality enhances process flexibility, allowing the centrifuge to adapt to changing feed compositions and regulatory requirements with ease.
Versatile Applications of 3-Phase Decanter Centrifuges
While the 3-phase decanter centrifuge is particularly effective in oily sludge treatment, its applications extend far beyond this field:
- Food and Beverage Processing: It is used for the separation of fats, oils, and solids in dairy, edible oil, and starch production.
- Chemical and Pharmaceutical Manufacturing: It aids in the purification of emulsions, recovery of catalysts, and separation of byproducts.
- Municipal Wastewater Treatment: It is employed for dewatering sewage sludge and separating grease from wastewater streams.
- Mining and Mineral Processing: It facilitates the recovery of valuable minerals from slurries and dewatering of tailings.
In all these applications, the GNLWS554's dual-motor drive, wear-resistant components, and intuitive interface control contribute to unparalleled efficiency and reliability.
As industries worldwide grapple with increasingly stringent environmental regulations and rising operational costs, GN Separation offers a sustainable and cost-effective alternative to conventional waste management practices. For further information, please visit the GN website and contact us.
- Details
-
Published: 27 June 2025
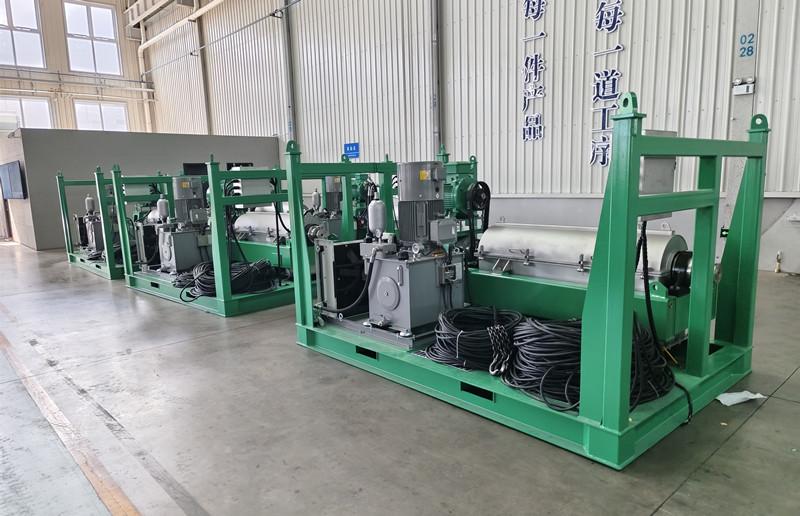
GN Separation is proud to announce the successful delivery of five GNLW364-FHD Full Hydraulic Drive Decanter Centrifuges to an overseas starch processing facility. These machines are designed to handle high-viscosity, high-concentration materials such as starch slurry, while also meeting stringent food-grade requirements.
- Details
-
Published: 20 June 2025
GN Separation has recently completed the production of a batch of hydraulic-driven decanter centrifuges, specifically the GNLW364-FHD model, for an overseas starch processing plant. These centrifuges, powered by Viscotherm's renowned hydraulic technology, deliver efficient and sustainable solid-liquid separation, particularly in high-viscosity applications.
How a Hydraulic Decanter Centrifuge Works
A hydraulic decanter centrifuge is a fundamental component in industries that rely on continuous solid-liquid separation. It harnesses centrifugal force to separate suspended solids from liquids based on their density differences. Here's a breakdown of its operation:
- Feed Introduction: The process commences with the introduction of slurry, such as starch slurry, into the rotating bowl through a stationary feed tube.
- Centrifugal Sedimentation: As the bowl rotates at high speeds (typically between 2,000 and 4,000 RPM), centrifugal forces up to 3,000×G propel denser solids towards the bowl's wall, while the lighter liquid forms an inner layer.
- Conveyor Mechanism: A screw propeller, rotating at a slightly different speed than the bowl, transports the settled solids towards the conical end for discharge.
- Phase Separation: Clarified liquid exits through adjustable weirs at the cylindrical end, enabling precise control over separation efficiency.
In hydraulic drive systems, the rotational motion of the bowl and screw is primarily or partially driven by hydraulic motors. Unlike traditional mechanical gearboxes, hydraulic systems offer variable speed control and dynamic torque adjustment, optimizing performance even under fluctuating feed conditions.
Advantages of Hydraulic Drive Systems
The GN centrifuge employs Viscotherm's hydraulic drive system, a hybrid design that integrates hydraulic and mechanical elements. This configuration offers several benefits, especially for high-viscosity and high-concentration materials:
- Stable Torque Output: The hydraulic drive ensures smooth and efficient operation, minimizing vibration and noise while enhancing separation efficiency and stability.
- Accurate Differential Control: The hydraulic differential allows for precise control, even at extremely low differential speeds, making it ideal for applications requiring high separation accuracy.
- Adaptability to Harsh Conditions: With robust heat dissipation and sealing, the hydraulic system operates reliably in high-temperature and high-humidity environments.
- Stable Sealing Performance: The system's sealing design effectively isolates contaminants, preserving oil purity and minimizing downtime due to malfunctions.
- Compact and Lightweight Design: The hydraulic differential is smaller and lighter than mechanical alternatives, reducing stress on main bearings and contributing to the overall longevity of the equipment.
Applications of Hydraulic Decanter Centrifuges
Hydraulic decanter centrifuges are highly versatile and find applications across various industries, including:
- Starch Production: Efficiently separating solids from liquids in starch processing.
- Wastewater Treatment: Removing solids from wastewater to comply with environmental standards.
- Chemical & Pharmaceutical: Ensuring product purity in chemical and pharmaceutical manufacturing processes.
- Mining & Minerals: Separating valuable minerals from ore slurries.
GN Separation's hydraulic decanter centrifuge, with its precise control and robust performance, is an excellent choice for a wide range of high-viscosity applications. For more information about GN's decanter centrifuges or to discuss your specific requirements, please don't hesitate to contact us.
- Details
-
Published: 20 June 2025